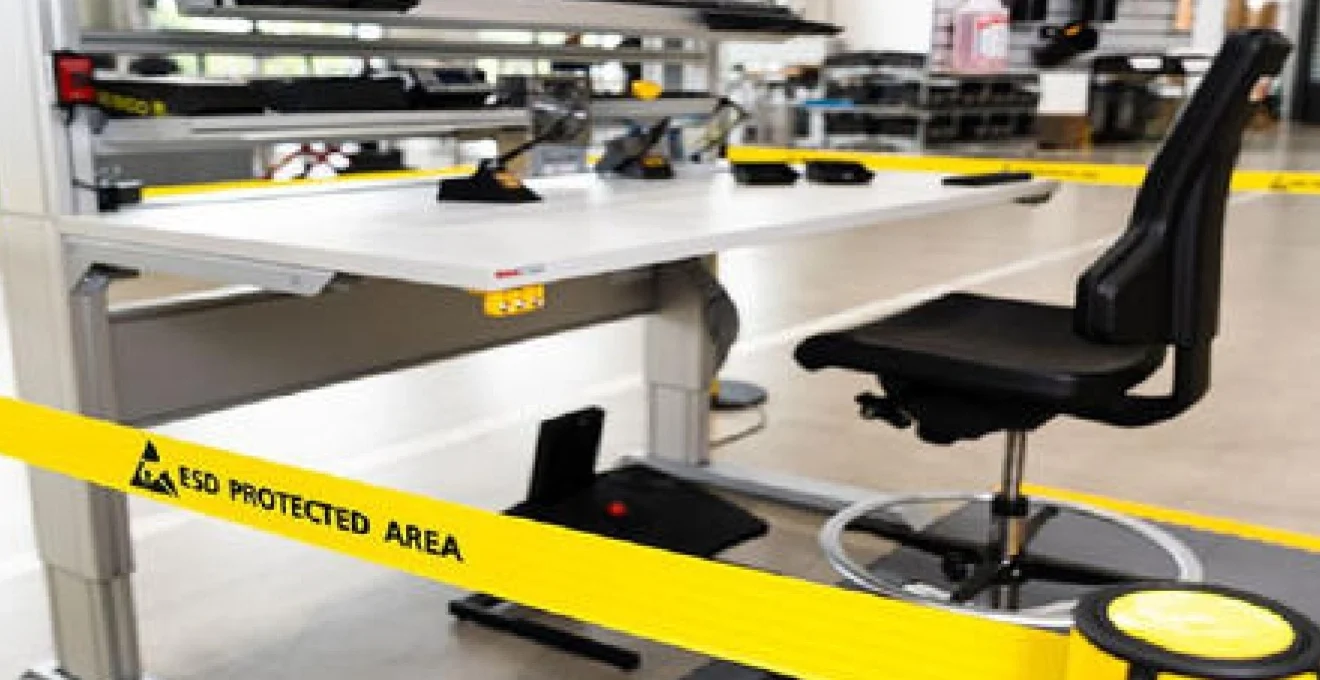
Electrostatic discharge (ESD) poses a significant threat to the electronics manufacturing industry. As electronic components become increasingly sensitive and miniaturized, the need for robust ESD protection measures has never been more critical. Implementing effective ESD protected area requirements is essential for safeguarding delicate components and ensuring the reliability of finished products. This comprehensive guide delves into the intricacies of ESD protection, exploring the fundamental principles, requirements, and best practices that are important for creating and maintaining a safe manufacturing environment.
The fundamentals of ESD protection
To fully grasp the importance of ESD protection in electronics manufacturing, it's essential to understand the underlying principles and potential risks associated with electrostatic discharges. By comprehending these fundamentals, you can better appreciate the necessity of implementing stringent ESD control measures in your manufacturing processes.
Understanding the phenomenon of electrostatic discharges
Electrostatic discharge occurs when there is a sudden flow of electricity between two electrically charged objects. This phenomenon is caused by the imbalance of electrons on the surface of materials. When two objects with different electrical potentials come into contact or close proximity, a rapid transfer of electrons takes place to equalize the charge. This transfer can generate voltages ranging from a few hundred to several thousand volts, depending on various factors such as humidity, material properties, and the nature of the contact.
In everyday life, you might experience ESD as a small shock when touching a doorknob after walking across a carpeted floor. However, in the realm of electronics manufacturing, even minuscule discharges that are imperceptible to humans can cause significant damage to sensitive components. The invisible nature of these discharges makes them particularly insidious, as the damage may not be immediately apparent but can lead to device failure over time.
The risks associated with ESD discharges in the electronics industry
The consequences of ESD events in electronics manufacturing can be severe and far-reaching. Some of the primary risks include:
- Immediate component failure
- Latent defects that manifest over time
- Reduced product reliability and lifespan
- Increased production costs due to rework and replacements
- Damage to brand reputation due to product failures in the field
The financial impact of ESD-related issues can be staggering. Industry estimates suggest that ESD damage costs the electronics industry billions of dollars annually in lost production, rework, and customer returns. As components become more sensitive to ESD, with some modern devices susceptible to discharges as low as 50 volts, the importance of comprehensive ESD protection strategies cannot be overstated.
Electrostatic discharge protection standards
To address the challenges posed by ESD, various international standards and guidelines have been developed. These standards provide a framework for implementing effective ESD control programs in electronics manufacturing environments. Some of the key standards include:
- ANSI/ESD S20.20 - Protection of Electrical and Electronic Parts, Assemblies and Equipment
- IEC 61340-5-1 - Protection of electronic devices from electrostatic phenomena
- MIL-STD-1686 - Electrostatic Discharge Control Program for Protection of Electrical and Electronic Parts, Assemblies and Equipment
These standards outline specific requirements for ESD control programs, including the establishment of ESD protected areas (EPAs) , personnel grounding procedures, and the use of ESD-safe materials and equipment. Adherence to these standards is important for maintaining a consistent level of ESD protection across the industry and ensuring the reliability of electronic products.
Requirements for ESD-protected areas
Creating an effective ESD-protected area is a cornerstone of any comprehensive ESD control program. These designated zones are specifically designed to minimize the risk of electrostatic discharge and protect sensitive electronic components throughout the manufacturing process. Let's explore the key requirements and considerations for establishing and maintaining an EPA.
Design criteria for ESD areas
When designing an ESD-protected area, several critical factors must be taken into account to ensure its effectiveness:
- Clearly defined boundaries: The EPA should have well-marked boundaries to indicate where ESD protection measures are in effect.
- Controlled access: Entry and exit points should be limited and controlled to maintain the integrity of the protected environment.
- Grounding infrastructure: A robust grounding system is essential for dissipating static charges safely.
- Environmental controls: Humidity and temperature should be carefully regulated to minimize static generation.
- Proper flooring: ESD-dissipative flooring materials should be used throughout the EPA.
The layout of the EPA should also consider the flow of materials and personnel to minimize the risk of ESD events. Workstations should be arranged to allow for efficient movement while maintaining ESD protection at all times. Remember, the goal is to create an environment where all surfaces, objects, and people are maintained at the same electrical potential, effectively neutralizing the risk of damaging electrostatic discharges.
The equipment required for an ESD zone
Equipping an ESD-protected area with the right tools and materials is important for maintaining a safe environment for handling sensitive electronics. Some essential equipment includes:
- ESD-safe workstations and furniture
- Grounding systems (e.g., wrist straps, heel grounders)
- Ionizers to neutralize static charges on insulators
- ESD-safe packaging materials
- ESD monitoring and testing equipment
Each piece of equipment plays a vital role in the overall ESD protection strategy. For instance, ESD-safe workstations provide a controlled surface for handling components, while ionizers help neutralize charges on non-conductive materials that cannot be grounded directly. It's important to select equipment that complies with relevant ESD standards and is appropriate for your specific manufacturing processes.
Monitoring and maintenance measures
Establishing an EPA is only the first step; ongoing monitoring and maintenance are important to ensure its continued effectiveness. Regular checks and audits should be conducted to verify that all ESD protection measures are functioning as intended. This includes:
- Daily verification of personnel grounding equipment
- Regular testing of ESD flooring and work surfaces
- Periodic calibration of ESD monitoring devices
- Routine inspections of ESD-safe packaging and handling procedures
Additionally, it's important to establish a system for tracking and documenting these maintenance activities. This not only helps in identifying potential issues before they become problematic but also provides valuable data for continuous improvement of your ESD control program.
Effective ESD protection is not a one-time implementation but an ongoing process that requires vigilance and commitment to maintain the highest standards of safety for sensitive electronic components.
Good practices for ESD risk management
Implementing good practices for ESD risk management is essential for creating a comprehensive and effective ESD control program. These practices go beyond the basic requirements and help create a culture of ESD awareness and prevention throughout your organization.
Conductive and antistatic materials in ESD areas
The selection and use of appropriate materials within the EPA are important for maintaining an ESD-safe environment. Conductive and antistatic materials play a vital role in dissipating static charges and preventing charge build-up. Some key considerations include:
- Using conductive or dissipative materials for work surfaces, flooring, and storage containers
- Implementing antistatic curtains or dividers to isolate sensitive areas
- Selecting ESD-safe chairs and seating options
- Utilizing proper ESD-safe cleaning products to maintain the protective properties of surfaces
It's important to note that not all antistatic materials are created equal. Some materials may lose their protective properties over time or under certain environmental conditions. Regular testing and replacement of these materials should be part of your maintenance routine to ensure consistent ESD protection.
Procedures for personnel and equipment
Establishing clear procedures for personnel and equipment handling is critical for maintaining the integrity of your ESD-protected area. These procedures should cover:
- Proper use of personal grounding equipment (e.g., wrist straps, heel grounders)
- Protocols for entering and exiting the EPA
- Handling and storage of ESD-sensitive devices
- Use and maintenance of ESD-safe tools and equipment
- Proper packaging and transport of sensitive components
Training is an important aspect of implementing these procedures effectively. All personnel who work within or interact with the EPA should receive comprehensive ESD awareness training. This training should cover the basics of ESD, the potential risks to electronic components, and the specific procedures and equipment used in your facility.
Regular checks to ensure compliance
Maintaining a high level of ESD protection requires ongoing vigilance and regular checks to ensure compliance with established procedures and standards. Some key elements of a robust compliance checking system include:
- Daily checks of personal grounding equipment
- Weekly or monthly audits of the EPA and its equipment
- Periodic third-party assessments of your ESD control program
- Continuous monitoring of environmental conditions (e.g., humidity, temperature)
Implementing a system of regular audits and compliance checks not only helps identify potential issues before they become problematic but also reinforces the importance of ESD protection to all personnel. Consider using digital tools and software to streamline the audit process and maintain accurate records of compliance activities.
Remember, the goal of these checks is not to punish non-compliance but to identify areas for improvement and ensure the ongoing effectiveness of your ESD control program.
Compliance with ESD regulations and certifications
Ensuring compliance with ESD regulations and obtaining relevant certifications is important for maintaining the credibility and effectiveness of your ESD control program. This section explores the key standards, certification processes, and legal considerations related to ESD management in electronics manufacturing.
ISO certifications and IEC standards relating to ESD
Several international standards and certifications are relevant to ESD control in electronics manufacturing. Some of the most important include:
- ISO 9001: Quality Management Systems
- IEC 61340-5-1: Protection of electronic devices from electrostatic phenomena
- ANSI/ESD S20.20: Protection of Electrical and Electronic Parts, Assemblies and Equipment
These standards provide a framework for implementing and maintaining effective ESD control programs. Achieving certification to these standards demonstrates your commitment to quality and ESD protection to customers and stakeholders. The certification process typically involves a thorough audit of your ESD control program, including documentation review, on-site inspections, and verification of compliance with specific requirements.
Audits and inspections to guarantee safety
Regular audits and inspections are essential for maintaining the effectiveness of your ESD control program and ensuring ongoing compliance with relevant standards. These assessments can be conducted internally or by third-party auditors, depending on your specific requirements and certification needs.
A typical ESD audit might include:
- Review of ESD control program documentation
- Inspection of ESD-protected areas and equipment
- Verification of personnel training records
- Testing of ESD control measures (e.g., surface resistivity, grounding systems)
- Assessment of ESD-safe handling procedures
The results of these audits should be carefully documented and used to drive continuous improvement in your ESD control practices. Any non-conformities or areas for improvement identified during the audit should be addressed promptly to maintain the integrity of your ESD protection measures.
Legal responsibilities in ESD management
Understanding and fulfilling your legal responsibilities related to ESD management is important for protecting your business and ensuring the safety of your products. While specific legal requirements may vary depending on your location and industry, some general considerations include:
- Compliance with relevant industry standards and regulations
- Proper documentation of ESD control measures and procedures
- Adequate training and certification of personnel
- Proper handling and disposal of ESD-sensitive materials
It's important to consult with legal experts familiar with ESD regulations in your industry to ensure that you're meeting all necessary requirements. Additionally, consider implementing a comprehensive risk management strategy that addresses potential liabilities related to ESD events and product failures.
By maintaining rigorous compliance with ESD regulations and standards, you not only protect your business from potential legal issues but also demonstrate your commitment to producing high-quality, reliable electronic products. This commitment can be a significant differentiator in the competitive electronics manufacturing landscape, helping you build trust with customers and partners alike.